
The Sintering Process of Iron Ore Fines – IspatGuru
Sintering is a thermal process (carried out at 1300 deg C to 1400 deg C) by which a mixture of iron ore, return fines, recycled products of the steel plant industry (such as mill scale, blast furnace dusts, etc.), slag forming elements, fluxes and coke fines are agglomerated in a sinter plant with the purpose of manufacturing a sintered product of a suitable stone composition, quality ...

Ore Sintering - an overview | ScienceDirect Topics
02-04-2010 · Like other sintering processes, iron ore sintering converts iron ore fines of often − 8 mm sizing into larger agglomerates, namely, sinter, between 5 and 50 mm particle size, which possess the physical and metallurgical characteristics and gas permeability required for efficient blast furnace operation. As shown in Figure 14.1, iron ore sintering is carried out in three stages: raw material ...

Sinter plant - Wikipedia
Sinter plants agglomerate iron ore fines (dust) with other fine materials at high temperature, to create a product that can be used in a blast furnace.The final product, a sinter, is a small, irregular nodule of iron mixed with small amounts of other minerals. The process, called sintering, causes the constituent materials to fuse to make a single porous mass with little change in the stone ...

sintering of iron ore fines in steel plant
Sintering is the most economic and widely used agglomeration process to prepare iron ore fines for blast furnace use In this chapter, the sintering process is first described and the key steps of the sintering process, namely, granulation and thermal densification, are identified...

What Is Iron Ore Sintering? (with pictures)
11-05-2020 · Specifically, iron ore sintering requires the use of fine ore, produced by crushing high-grade iron ore into particles only a few millimeters in diameter. Depending on the specific machine and iron ore sintering process used, substances such as coke breeze and burnt limestone are used to ignite and heat the iron ore particles until the particles congeal.

(PDF) Iron Ore Sintering: Process - researchgate.net
Sintering is a thermal agglomeration process that is applied to a mixture of iron ore fines, recycled ironmaking products, fluxes, slag-forming agents and solid fuel (coke).

Sintering: A Step Between Mining Iron Ore and …
World resources are estimated to be greater than 800 billion tons of crude ore containing more than 230 billion tons of iron. The only source of primary iron is iron ore, but before all that iron ore can be turned into steel, it must go through the sintering process. Sinter is the primary feed material for making iron and steel in a blast furnace.

sintering of iron ore fines in steel plant - Mine …
Sale of iron ore fines by the iron ore lessees. - Odisha Minerals ... Department of Steel & Mines, Odisha, Bhuhaneswar. Sub:- Sale of ... of iron ore fines to the sponge iron ore plants by various mine owners. In this regard it ... Ii used only by Pelletizing plant or Sintering plant. it the fines …

Melting Characteristics of Iron Ore Fine During …
01-05-2011 · Except Issue 5 Melting Characteristics of Iron Ore Fine During Sintering Process 13 - Fig. 3 Relationship between relative height of sample and temperature t 01 I I b 1273 1473 1673 Temperat ixdK Fig. 4 Typical melting curves of iron ore ore A2, the melting curve of iron ore has three steps as iron ore begins to melt, which are “rapid shrink- ing†firstly, then “slow ...

CHAPTER-11 FUNDAMENTALS OF IRON ORE SINTERING
FUNDAMENTALS OF IRON ORE SINTERING R. P. Bhagat INTRODUCTION The process of sinter making originated from a need to make use of fines generated in mines and in ore benefiCiation plants. With the development of sintering technology, a sintering plant has become a tremendous success for providing a phenomenal increase in
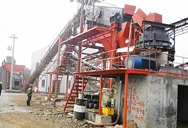
Iron Ore Fines Size For Sintering - sport-hippique.nl
Influence of Iron Ore Fines Feed Size on Microstructure . the iron ore feed size in sintering process. In present inves-tigation pot grate sintering experiments were carried out with various size iron ore fines (1.22 to 3.95 mm mean size) to study the influence of iron ore feed size on properties and productivity of …

Iron Ore Agglomeration Processes and their …
These micro fines of high-grade concentrates had to be agglomerated for their use in the blast furnace and this has led to the development of the pelletizing process. These agglomerates, in turn, sharply improved blast furnace performance and led to a major shift in blast furnace burdening. History of sintering of iron ore

Sintering studies of Iron Ore Fines of Hospet-Sandur ...
Iron ore fines from M/s H R G mines of Donimalai range generated from the crushing/screening plant were collected for taking up the sintering studies. Representative sample of iron ore fine was drawn for the bulk quantity received and was subjected to stone analysis and …

SINTERING AND PELLETISATION OF INDIAN IRON ORES
High grade iron ore less than 10% of the total reserves. ROM iron ore with Fe less than 58 – 60% discarded as waste. After beneficiation iron ore availability can improve by about 50%. Steel community and the country demand technological solutions for utilising low grade ores. The technology task that would be imperative: 1.

Iron Ore Pelletizing Vs Sintering - mariniers-qpo.nl
Iron ore sinter pellet - garagecoene.The difference between pelletizing and sintering, the difference between pelletizing and sintering production processes 1with the continued exploitation of the earths resources, a shortage of high-grade ore, lean ore must constantly expand the use of resources, and the beneficiation technology can be economically selected high-grade iron ore fine.

Modeling Sintering Process of Iron Ore
Modeling Sintering Process of Iron Ore Jose Adilson de Castro Graduate Program on Metallurgical Engineering -Federal Fluminense University Brazil 1. Introduction In this chapter, a methodology for simulating th e sintering process of iron ore is presented. In order to study the process parameters and inner phenomena, a mathematical model

sintering of iron ore fines in steel plant
The Sintering Process of Iron Ore Fines IspatGuru. Mar 09, 2013 Sintering process helps utilization of iron ore fines (0-10 mm) generated during iron ore mining operations; Sintering process helps in recycling all the iron, fuel and flux bearing waste materials in the steel plant.

Iron Ore Fines Agglomeration
iron ore agglomeration mill - grill-restaurant-zagreb.de. Agglomeration Of Ore Fines - . Grinding Mill. grinding mills vary from coarse grinding, medium grinding to micro fine grinding.Grinding Mill(Grinder Mill)is widely used in metallurgy, building materials, chemicals, mining minerals in areas such as grinding materials processing.The materials include line, calcite, barite, coal ...
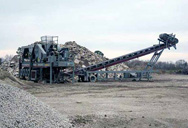
sintering process of iron ore - …
Sintering plant at a glanceOct 27, 2014· •The granulometry of iron ore fines, used in sintering, has a great influence on sinter plant performance •Laboratory Experiments were conducted with different granulometry of iron ore fines to assess its influence on sinter quality and productivity •The upper size of the iron ore fines was reduced in each of the experiments.Iron process ...