
Jaw Crusher - an overview | ScienceDirect Topics
Hence, the crusher jaws produced with austenitic manganese in these conditions eradicated brittle failure experienced in locally produced crusher jaws. 4. Hardening followed by tempering precipitated carbide at the stone boundaries and in the grains instead of reducing the residual stress associated with hardening.

Iron Ore Crushing Process Before Crusher Hardening
Iron Ore Crushing Process Before Crusher Hardening. With picturesJan 12 2020 Iron ore mining often focuses on looking for hematite deposits known as red iron ore and magnetite as they have naturally weak magnetic fields that aid in their purification Hematite however responds better to the flotation process in iron ore beneficiation than magnetite so it is the preferred type of ore.
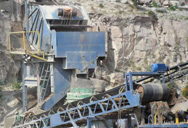
Jaw Crusher Cmade Of Hardened Manganese Steel
Jaw crusher made of hardened manganese steeligh manganese steel is the traditional material jaw crusher jaw, which has good toughness, also has good deformation hardening material uses mn13, mn13cr2, mn18, mn18cr2 ultra-high manganese or special ingredients according to working conditions, hubei jys production of. get price

tab of the jaw crusher - minimaalroyaal.nl
jaw crusher hardening - Minevik >C6X Series Jaw Crusher >HPT Series High-Efficiency Hydraulic Cone Crusher >Spring Cone Crusher >CI5X Series Impact Crusher PRODUCTS >HPT Cone Crusher >B Series VSI Crusher RELATED >Trapezium Mill >Raymond Mill jaw crusher hardening R Crusher , More; STURTEVANT 2 X 6 Jaw Cr - 311377 For Sale Used N/A

jaw crusher hardening - Seaforth Lodge
Jaw crushers, Impact crushers, and Cone crushers for rock, concrete, stone, glass and more The Deformation, Strain Hardening, and Wear Behavior of In this work, the impact and abrasive properties of a chromium-alloyed high-manganese Hadfield steel were experimentally studied using a wide variety of testing techniques and characterization methods.
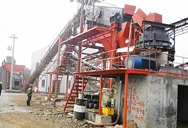
Workhardening Behaviour and Microstructural Analysis of ...
crusher jaw (S) and failed crusher jaws (F 1, F 2, F 3 and F 4) are presented in Table 1. The Brinell hardnesses at various case depths are presented in Figure 2 to 5. The impact strengths for both sound and failed crusher jaws are presented in Figure 6. The observed microstructures of the samples are shown in Figures 7 to 14.

Cone Crusher Hardening - landhotel-reiterhof.de
Cone Crusher Hardening. The most efficient cone crusher on the market The Sepro Blackhawk 100 Cone Crusher is a modern hydraulically operated cone crusher designed to be simple rugged and effective for heavy duty mining and aggregate applications The combination of the speed and eccentric throw of the crusher provides fine crushing capability and high capacity in a very compact design

Hardening of crasher cement ball - grenzgaenger …
hardening of crasher cement ball used coal jaw crusher for rapid hardening of cement by the of normal setting or ordinary or portland cementthese balls roll within the mill and get more info jaw crusher made of hardened manganese. Get Price. Email [email protected]

Jaw Crushers | McLanahan
Jaw Crushers are used to reduce the size of many different types of materials in many applications. The Jaw Crusher was first introduced by Eli Whitney Blake in 1858 as a double-toggle Jaw Crusher. Introduced in 1906, McLanahan’s Universal Jaw Crusher was one of the first modern era overhead eccentric Jaw Crushers.

R Crusher Wear Parts Reference Guide
crusher tools E.G. Jaw liners are subject to numerous pressure and impact stresses. Several other factors affect the wear lifetime of crusher wear parts as listed in below Diagram . Wear occurs in all crushers , however wear costs can be controlled by selecting the correct crusher type for the abrasive content of the material to be crushed.

Jaw Crusher Unicast - HeNan Mining Heavy …
Unicast jaw crusher wear parts are cast using M2 M19 or M22work hardening alloys for optimum performance. Titanium Carbide TiC options are available for even longer wear life. Custom designed to suit your needs Unicast Jaw Plates and Cheek Plates are engineered to suit the specific needs of your application. Features Benefits

liming C series jaw crushers Wear parts application guide
In crushers like C105 and C3055, the jaw die design on the ends is different. The lock-ing wedges on these crushers are located behind the jaw dies rather than at the top of the jaw die. Jaw dies can be allowed to wear until the thickness is 60 to 65 mm thick, or the teeth are worn flat. On other crushers the ends of the jaw dies are much thinner.

jaw crusher running - dietisthoofddorp.nl
Jaw crusher speed must run slow enough for the Jaw liners to bite the material but not too fast that the material rubs the jaw liner teeth. Early rotation of the Jaw liners will assist in work hardening . Chat Now. Getting The Most Out Of Your Jaw Crusher - Pilot Crushtec.

Workhardening behaviour and microstructural …
The hardness values of failed crusher jaw samples were higher than that of sound crusher jaws from the working surface to the depth of 95 mm while it is lower from depth of 50 mm to 120 mm (Figures 2 to 5). This hardness gradient indicates that there is no uniform stone flow during work hardening of failed crusher jaws.

Heat Treatment For Jaw Crusher Body Plate
High Manganese Steel Mn14 Jaw Crusher Toggle. We choose the right materials and process for customers according to the users working conditions, such as the hardness, fragile degree of ore, specifications of the jaw crusher parts and etc.Pe400600 coarse jaw crusher, main consideration of the material is the toughness and work hardening rate pe250400 and pex series of jaw crusher, while …

Jaw Crusher|Crusher Wear Parts Jaw Plate
Jaw Crusher Wear Parts Replacement Jaw Plates Cheek, Unicast jaw crusher wear parts are cast using m2 m19 or m22work hardening alloys for optimum performance titanium carbide tic options are available for even longer wear life custom designed to suit your needs unicast jaw plates and cheek plates Crusher Wear Parts Jaw Plate

Crusher - Wikipedia
A crusher is a machine designed to reduce large rocks into smaller rocks, gravel, sand or rock dust.. Crushers may be used to reduce the size, or change the form, of waste materials so they can be more easily disposed of or recycled, or to reduce the size of a solid mix of raw materials (as in rock ore), so that pieces of different composition can be differentiated.