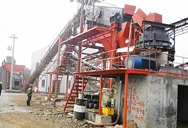
Advanced Process Control for Optimizing Flue Gas ...
Wet Limestone Scrubbing Process Description. Figure 1 depicts a flow diagram for a typical wet limestone scrubbing flue gas desulfurization (FGD) process.Sulfur dioxide (SO 2) contained in the flue gas is absorbed by a limestone slurry sprayed from the header at the top of the absorber.
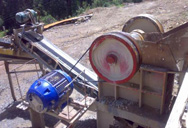
Technology Optimization of Wet Flue Gas …
Optimization of the wet limestone (calcite) flue gas desulfurization (FGD) process is described, with the focus on the layout of subprocesses and equipment.
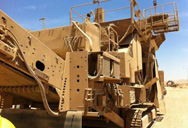
Dynamic optimization oriented modeling and …
1-3-2020 · Based on the models of the wet limestone FGD system, numerous advanced control algorithms were applied to improve optimal control performance, such as neighboring extremal control , real-time optimization method , real-time iterations strategy , model predictive control (MPC) with incomplete optimization , real-time nonlinear optimization strategy , best optimal performance …
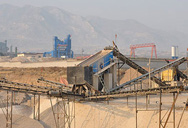
Flue Gas Desulfurization Optimization | WWD
CWLP provides electricity to the city of Springfield, Illinois, from four coal-fired units complete with wet FGD systems to remove sulfur dioxide (SO2) from the boiler (flue) gas produced during coal combustion. Limestone reagent slurry with greater than 95% calcium carbonate reacts with the SO2 entering the FGD system with the flue gas.
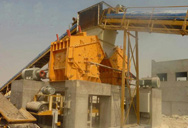
Advanced Process Control for Optimizing Flue Gas ...
31-10-2018 · Coal-fired power plants can significantly improve wet limestone scrubbing with advanced process control. One optimization system implemented …
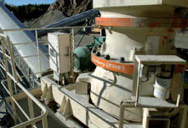
wet fgd optimization - Birthing Naturally
wet fgd optimization. 300MW_ Operation Optimization on Wet FGD System of 300 MW Coalfired Unit in ShaoGuan Power Plant TAN Chaohong (ShaoGuan Power Plant, Shaoguan 512132,China) ...
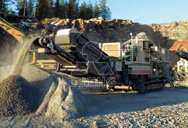
Dynamic optimization oriented modeling and …
Dynamic optimization oriented modeling and nonlinear model predictive control of the wet limestone FGD system. ... To equipoise the models accuracy and conciseness, the wet limestone FGD system is separated into several modules. Based on the conservation laws, ...
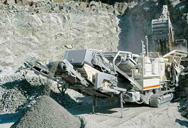
Benefit Analysis and FGD Optimization for …
Benefit Analysis and FGD Optimization for Designed Power Plant Based on Comprehensive Benefit Index System p.255. Biodiesel Production ... For the index system with index of earning of by-product, the optimal FGD technology is wet ammonia desulphurization, ...
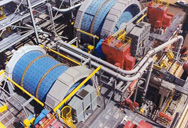
Model of the Wet Limestone Flue Gas …
19-5-2001 · A detailed process model of the wet limestone flue gas desulfurization system has been presented. This model can be used to calculate indispensable parameters for estimating costs and next to minimize capital and operating costs. The process model describes most important stage of SO2 removal running in an absorber and a holding tank.
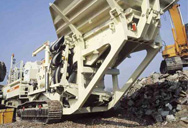
TECHNOLOGY
BHEL supplying MHPS wet limestone FGD system . BHEL commissioned seawater-based FGD at Trombay unit #8 250 MW of MHI Technology in 2010. It supplied Wet Limestone based FGD to NTPC Bongaigaon 3x250 MW of Ducon Technology in 2012. BHEL signed a TCA with MHPS for Wet FGD technology in April 2013.
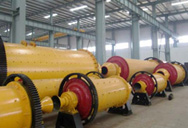
Selenium Speciation and Management in Wet FGD …
25-7-2020 · Synthetic gypsum produced by wet flue gas desulfurization (FGD) systems on coal-fired power plants is commonly used in the manufacture of wallboard. This practice has long benefited the environment by recycling the FGD gypsum byproduct, which is becoming available in increasing quantities, decreasing the need to landfill this material, and increasing the sustainable design of the …
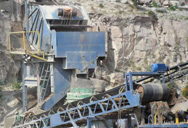
EFFICIENT PROCESSES Wet limestone grinding for FGD
FGD plants for limestone wet grinding we also care for the optimization of running operations or components – because as process specialists we are most familiar with a wide range of systems. Water Water Ball Mill Mill Slurry Tank Feed Bin
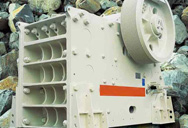
Performance optimization of wet flue gas …
Request PDF | Performance optimization of wet flue gas desulphurization system based on CFD technology | Based on the computational fluid dynamics (CFD) and unsteady mass transfer theory ...
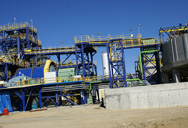
Wet Flue Gas Desulfurization with Seawater
Flow optimisation is therefore extremely necessary. In the mist eliminator, the drops carried from the absorption zone by the flue gas, are returned to the process. At the outlet of the absorber, the clean gas is saturated and can be directly removed via a cooling tower or wet stack. Optionally the clean gas can be heated and routed to a dry stack.
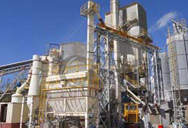
Model of the Wet Limestone Flue Gas …
A detailed process model of the wet limestone flue gas desulfurization system has been presented. This model can be used to calculate indispensable parameters for estimating costs and next to minimize capital and operating costs. The process model describes most important stage of SO2 removal running in an absorber and a holding tank. It includes absorption of sulfur dioxide, oxidation of SO3 ...
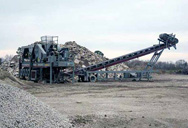
Scrubbing: Optimizing Flue Gas Desulfurization ...
31-8-2006 · New flue gas desulfurization (FGD) units are being installed at utilities in many parts of the U.S. and a large percentage of the new scrubbers are of the wet limestone type.

Technology Optimization of Wet Flue Gas …
Optimization of the wet limestone (calcite) flue gas desulfurization (FGD) process is described, with the focus on the layout of subprocesses and equipment. The aim of optimization was to check the effectiveness and reliability of alternative layouts, involving intermediate product (gypsum) storage in the absorber make‐up tank, instant production of limestone slurry from powder in a wet ...
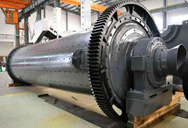
Crystallisation of Gypsum and Prevention of …
The results of this work can be used for the optimization of wet FGD-plants in terms of reliability of operation and consistency of the gypsum quality obtained. This work may furthermore be of interest to other industrial systems in which foaming or gypsum crystallisation may take place.
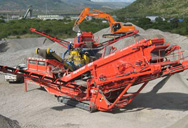
Optimization and system control of a wet flue gas ...
When an FGD system with a cross-sectional area of 30 m 2, an absorption tower of height 15 m and a water depth in the oxidation tank of 5 m was used to treat flue gas containing 1,000 ppm of SO 2 at a flow rate of 500,000 m 3 (STP)· h-1, we obtained the following optimum values: dissolved SO 2 concentration: under 0.001 kmol · m-3 (LGM), 0.05 kmol · m-3 (MHM); diameter of droplet: 1.5 mm ...